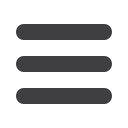
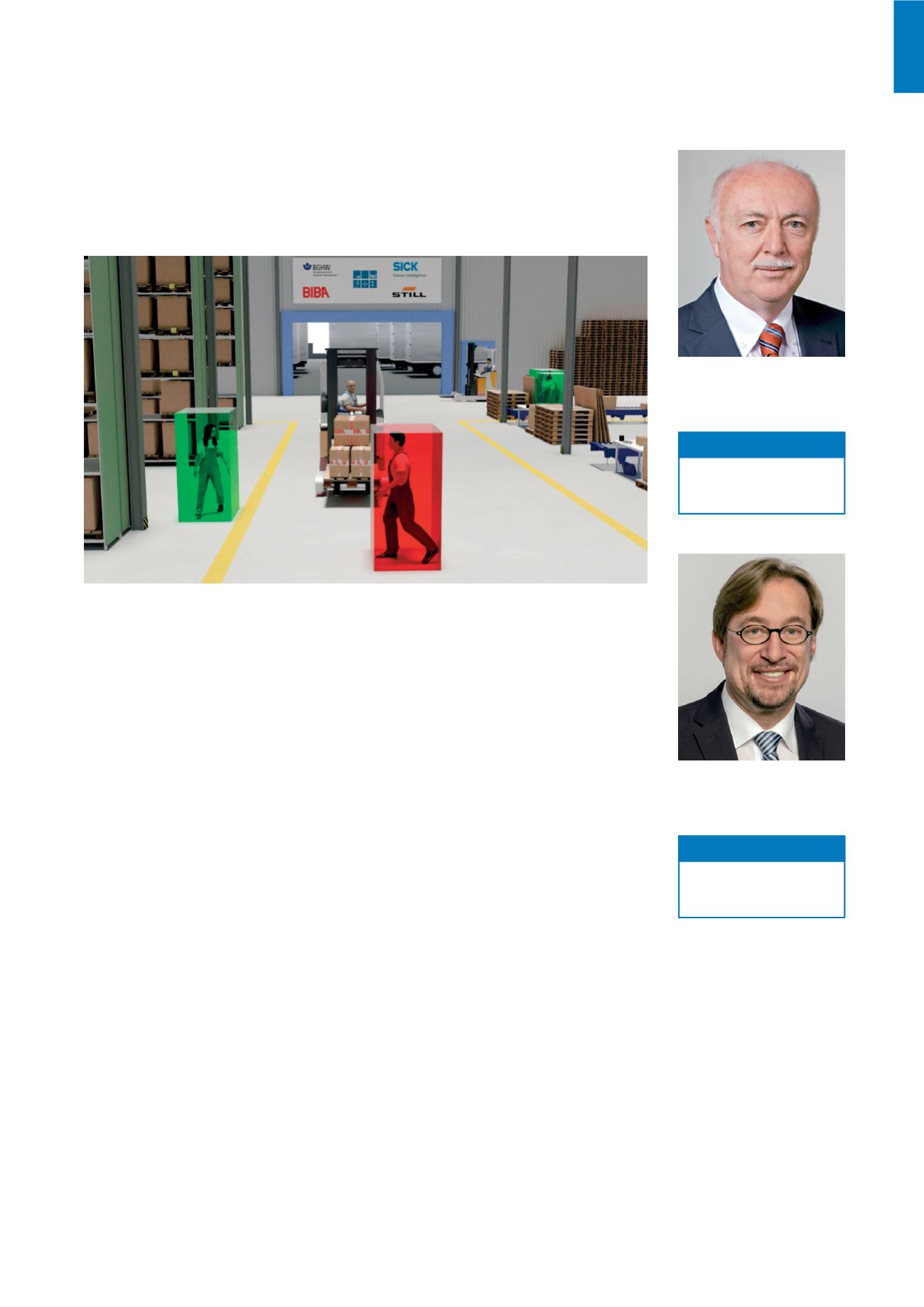
Materials Handling, Material Flow, Logistics
123
Materials Handling, Material Flow, Logistics/Technical Logistics
Basic and applied research in logistics engineering
Prof. Dr.-Ing. Dipl.-Wi.-Ing.
Willibald A. Günthner
Prof. Dr.-Ing.
Johannes Fottner
n
The Institute for Materials Handling, Material Flow and Logistics
perceives itself as an open research institution aiming to contribute to
scientific progress in the areas of material flow technology and logistics
engineering.
Taking into account current economic,
ecological, social and technological devel-
opments, such as continuing volatility of
the markets, changing demography and
technological innovations, the focus of the
institute is on designing adaptive/flexible,
sustainable and human-oriented/humane
logistics systems and technology. In the
project ‘PräVISION’, the Institute develops
a guidance system to warn fork lift drivers
www.fml.mw.tum.de kontakt@fml.mw.tum.dePhone +49.89.289.15921
Contact
www.fml.mw.tum.de kontakt@fml.mw.tum.dePhone +49.89.289.15921
Contact
against upcoming collisions. Due to the
drivers’ limited sight, many accidents
occur – often with human impact. A time-
of-flight camera delivers 2D and 3D data
independent of the environmental lighting.
Using state-of-the-art methods of com-
puter vision, these data are used to detect
people in real time and predict possible
accidents by calculating relative speeds.
The guidance system ‘PräVISION’ warns fork lift drivers against upcoming collisions
Innovative Conveyor Technology
Automated material handling systems
are widely used in industry due to high
throughputs and good process quality. In
order to fully utilize their potential, these
systems have to be custom-built, requiring
individually created control software.
The engineering process of the control
software includes extensive manual pro-
gramming, because a modular structure
of the control algorithm with predefined
modules is often missing. In the aComA
project (automatische Codegenerierung
für modular aufgebaute Anlagen) such a
modular control algorithm is developed,
based upon a two-layer architecture that
separates the hardware control from the
material flow control. The modular control
algorithm allows predefined modules for
both the conveyor hardware and material
flow elements to be created and then
assembled in the needed configuration.
As a result, the control software for a cus-
tom-built material handling system can be
created by arranging predefined modules
and setting their parameters, thus without
manual programming.