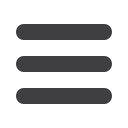
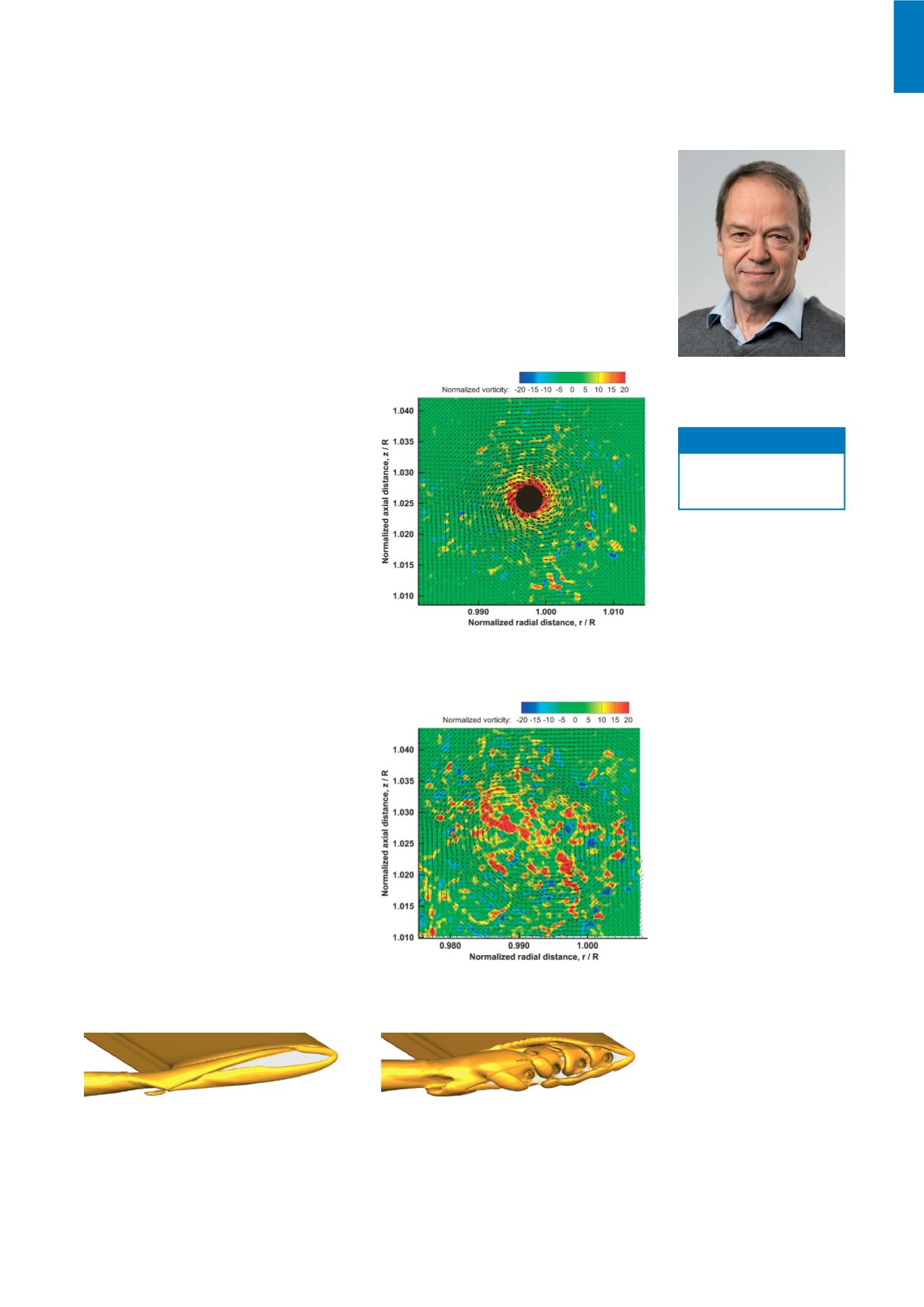
Helicopter Technology
137
Helicopter Technology
Performance, efficiency and safety for rotorcraft
Prof. Dr.-Ing.
Manfred Hajek
n
In 2016, the Institute has been appointed ‘Vertical Lift Research Center
of Excellence (VLRCOE)’ of the U.S. – as the first non-U.S. institution that
has been awarded this prestigious status. Partnering with the University
of Maryland, the University of Texas at Austin and the U.S. Naval Acad-
emy, HT will perform joint aerodynamics and dynamics research under
this 5-year program. A grant was awarded by the U.S. Office of Naval
Research – the first on rotorcraft research outside the U.S. – which is
contributing funding within their basic research program for the simulation
of helicopter ship deck landings.
www.ht.mw.tum.de office@ht.mw.tum.dePhone +49.89.289.16300
Contact
Passive Tip Vortex Control
In hover, descent and low-speed forward
flight, the vortices trailed from the main
rotor blade tips can interact with subse-
quent blades. This so-called blade-vortex
interaction (BVI) is associated with many
detrimental effects such as high vibration
and noise levels. These adverse effects
may potentially be mitigated by diffusing
these tip vortices. Therefore, in a joint
research project with the U.S. Naval
Academy, experiments and CFD simula-
tions were performed to investigate the
ability of model-scale centrifugal pumping
rotor blades to diffuse these tip vortices
by passively blowing air into the forming
vortex at the blade tip.
High-resolution particle image velocimetry
was used to gain insight into the flow
field generated during the initial vortex
formation process and phase-averaged
measurements were used to validate the
numerical simulations. It was found that
for early wake ages, spanwise blowing
effectively diffused the tip vortex. The
numerical simulations revealed details of
the vortex formation process at the blade
tip, as well as in the internal channel, that
cannot be measured experimentally.
As a result, areas for potential design
improvements were found.
Measured normalized instantaneous vorticity for the
baseline blades tip vortex close to the blade
Measured normalized instantaneous vorticity for the
centrifugal pumping blade tip vortex close to the blade
Visualization of Q criterion at the blade tip for the
baseline blade
Visualization of Q criterion at the blade tip for the
centrifugal pumping blade