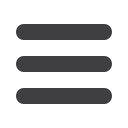

Lightweight Structures
157
Lightweight Structures
New structural concepts – structural simulation and design optimization methods –
experimental structural and material investigations
n
Highly flexible structures have been a major research focus in 2016,
looking also at suitable composite materials allowing such flexible struc-
tures to also undergo large shape variations and at the same time to take
considerable loads. A further focus of research was on the effects of
large thermal loads and thermal load cycles on structures. This not only
includes higher but also extremely low cryogenic temperatures such as
in lightweight liquid hydrogen tanks. The areas of application of these
and other research activities have been mostly in aerospace, but also in
automotive and special structures.
www.llb.mw.tum.de info@llb.mw.tum.dePhone +49.89.289.16103
Contact
Flexible Wing Demonstrator
– EU FLEXOP
The goal to develop aircraft which are
greener, safer, and more cost effective
can only be achieved with by significant
innovations in aircraft design methods.
Advanced aerodynamic and structural
design technologies can be achieved by
passive as well as active suppression of
aeroelastic instabilities. To demonstrate
the potential of this approach, an exper-
imental test platform with a high aspect
ratio (AR) wing and clearly predefined
flutter characteristics is developed within
the project FLEXOP. Therefore, methods
for accurate flutter prediction become
essential throughout the entire develop-
ment process.
The challenges for the structural wing
design are related to the conflicting design
goals of having an elastic wing with low
flutter speed but also allowing it to be stiff
and strong enough to sustain the maneu-
ver loading due to different flight opera
tions. Furthermore, important aeroelastic
side effects like rudder reversal, deforma-
tion-induced stall as well as divergence
have to be taken into account.
Due to the strong interaction between the
structural elasticity and the wing aerody-
namics, a coupled investigation is neces-
sary from an early point in the design task.
Therefore, the structural composite wing
design is implemented as a finiteelement
model, while steady and unsteady aerody-
namic forces are computed using efficient
potential flow theorybased approaches,
like the double-lattice method (DLM).
Since many configurations, parameter
variations and flight maneuvers have to
be studied in the early structural design
stage, this is a reasonable strategy for
obtaining rapid estimations of the struc-
tural loading, the demonstrator’s perfor-
mance and the aeroelastic behavior.
Univ.-Prof. Dr.-Ing.
Mirko Hornung
(interim)
1st asymmetric and 2nd symmetric wing flutter mode
FLEXOP demonstrator aircraft
Structural design of the AX-8 flutter wing