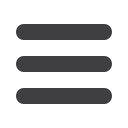

72
Aerodynamics and Fluid Mechanics
Prof. Dr.-Ing.
Nikolaus A. Adams
Aerodynamics and Fluid Mechanics
Numerical modeling, simulation and experimental analysis of fluids and fluid flows
n
The focus of the Institute of Aerodynamics and Fluid Mechanics in
2015-16 was on propulsion fluid dynamics, deriving new particle methods
for continuum mechanics, development of a multi-resolution parallel
simulation environment for the NANOSHOCK project, on reduced-order
modeling and control of rotary and fixed-wing aerodynamics, and on
advanced simulation technologies in automotive aerodynamics.
Cavitation and Flow-Induced Erosion
Motivation and Objectives
Flow-induced evaporation (cavitation) of
liquids occurs in a broad range of tech-
nical systems. In combustion engines,
cavitation is leveraged in order to control
the mass flow and to clean spray holes
from exhaust products. Collapsing vapor
bubbles may also be used to enhance
drug delivery in biomedical applications.
However, if vapor cavities collapse in an
induce strong noise and vibrations. Both
are highly undesirable for pumps and
turbines, as well as for naval vessels such
as cruise liners.
Our objective is to implement accurate
simulation approaches for predicting
all dominating phenomena in cavitating
flows, with the goal to provide the ground-
work for the design optimization of future
technical devices.
Approach to Solution
We develop mathematical models and
numerical approaches for efficient and
accurate prediction of cavitating flow
phenomena. The thermodynamic
description of all fluid components (liquid,
vapor, inert gases) involved makes for
compressible fluid models possible.
These enable the simulation of shock
wave formation due to collapsing vapor
patterns. Thereby, intense loads on
material surfaces are obtained without the
need for additional models. Depending
on the dominant physics, high-quality
shock-capturing schemes and large-eddy
simulation (LES) schemes are proposed
and applied to fundamental as well as to
highly practical problems. Fundamental
research is funded by the European Union,
while applied research is performed in
collaboration with automotive suppliers,
the U.S. Office of Naval Research and the
European Space Agency.
www.aer.mw.tum.de nikolaus.adams@tum.dePhone +49.89.289.16138
Contact
A highlight in 2015/16 was the successful
defense of the Collaborative Research
Program TRR 40 on propulsion systems
for space transportation which entered
its 3rd and final funding period 2016-
2020. The TRR 40 is one of the largest
fundamental research activities on this
subject worldwide. Dr. Daniel Gaudlitz,
formerly Senior Research Associate with
the Institute, was appointed as Professor
of Fluid Mechanics at the University of
Appliead Sciences in Zwickau.
Side- and top-view on a shedding
partial cavity forming past a sharp
wedge.
uncontrolled way, the surrounding material
can be severely damaged. Especially
for high pressure systems, such as fuel
injector components of automotive and
naval combustion engines, cavitation
erosion represents a continuous challenge
for designers. Violent collapses of vapor
patterns can result in the formation of
intense shock waves with amplitudes
reaching more than 10,000 bar – enough
to damage even stainless steel. In addition
to material removal, cavitation may also