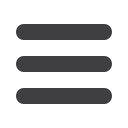

98
Carbon Composites
Carbon Composites
Fundamental research on material behavior, processing technology
and simulation of high performance composite materials
Prof. Dr.-Ing.
Klaus Drechsler
Process Technology for Fibers and Textiles
as a test bed for the industrial internet
environment ‘Industrie 4.0’ to explore the
potential for future CFRP production. A
great success in 2016 was the granting of
a DFG project that will be investigating the
implementation of fiber optical sensors in
the laminates within the AFP process.
n
As a highlight in 2016 the 17th European Conference on Composite
Materials (ECCM17) was organized by the Chair of Carbon Composites
and the leading-edge cluster MAI Carbon, under the patronage of the
European Society for Composite Materials (ESCM) from 26th-30th June
at the International Congress Center (ICM) in Munich. The conference
attracted more than 1,300 internationally renowned scientists and engi-
neers in the field of aerospace, automotive and mechanical engineering
and brought together the scientific and the application-oriented world. An
attractive supporting program was arranged to complement the interest-
ing presentations and discussions.
The ‘Process Technology for Fibers and
Textiles’ group focuses on improving
manufacturing technologies that arrange
fibers in their desired orientation within a
composite component.
The group’s three research teams cover the
fields of braiding technology, automated
fiber placement and tailored textiles. With
highly developed processing equipment,
the fibers can be brought into shape in an
automated and reproducible way.
Automated Fiber Placement
The Fiber Placement Center located on
the ‘Ludwig Bölkow Campus’ in Tauf
kirchen, that was set up last year, has
been brought into full operation. In 2016,
the Center’s capabilities for the automated
production of large components with
thermoset fiber placement were proven in
two major projects with partner compa-
nies from the aerospace industry.
Whereas thermoset fiber placement is
already widely used for making aerospace
parts, research in the field of thermoplas-
tic fiber placement is rather fundamental.
Current work (e.g. in the Accurat3 project)
is aiming to improve the 3D-capability of
the process to enable the manufacture of
complex components.
To further improve existing machines, addi-
tional systems have been implemented e.g.
for the online monitoring of process data
and product quality via optical and thermal
camera systems. The newly started project
‘ISP’ uses the automated production
equipment with these integrated sensors
www.lcc.mw.tum.de drechsler@lcc.mw.tum.dePhone +49.89.289.15092
Contact
Lay-up of thermoset prepreg tapes with an automated
fiber placement machine
Textile Preforming
On the textile preforming site at the
Forschungszentrum in Garching, new
draping equipment was set up. By using
a flexible membrane, complex carbon
fiber preforms can now be realized in
an automated and reproducible way. An
external heating unit with IR lamps acti-
vates thermoplastic binder in the material
to stabilize the preform. Automated
robot guided cutting enables guaranteed
high-accuracy final trimming of the formed
materials. Flat textiles can be combined
with braided or patched laminates to
generate preforms that are exactly tailored
to the desired application. All technologies
are used in both publicly-funded as well
as bilateral industrial projects.