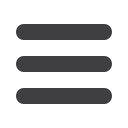
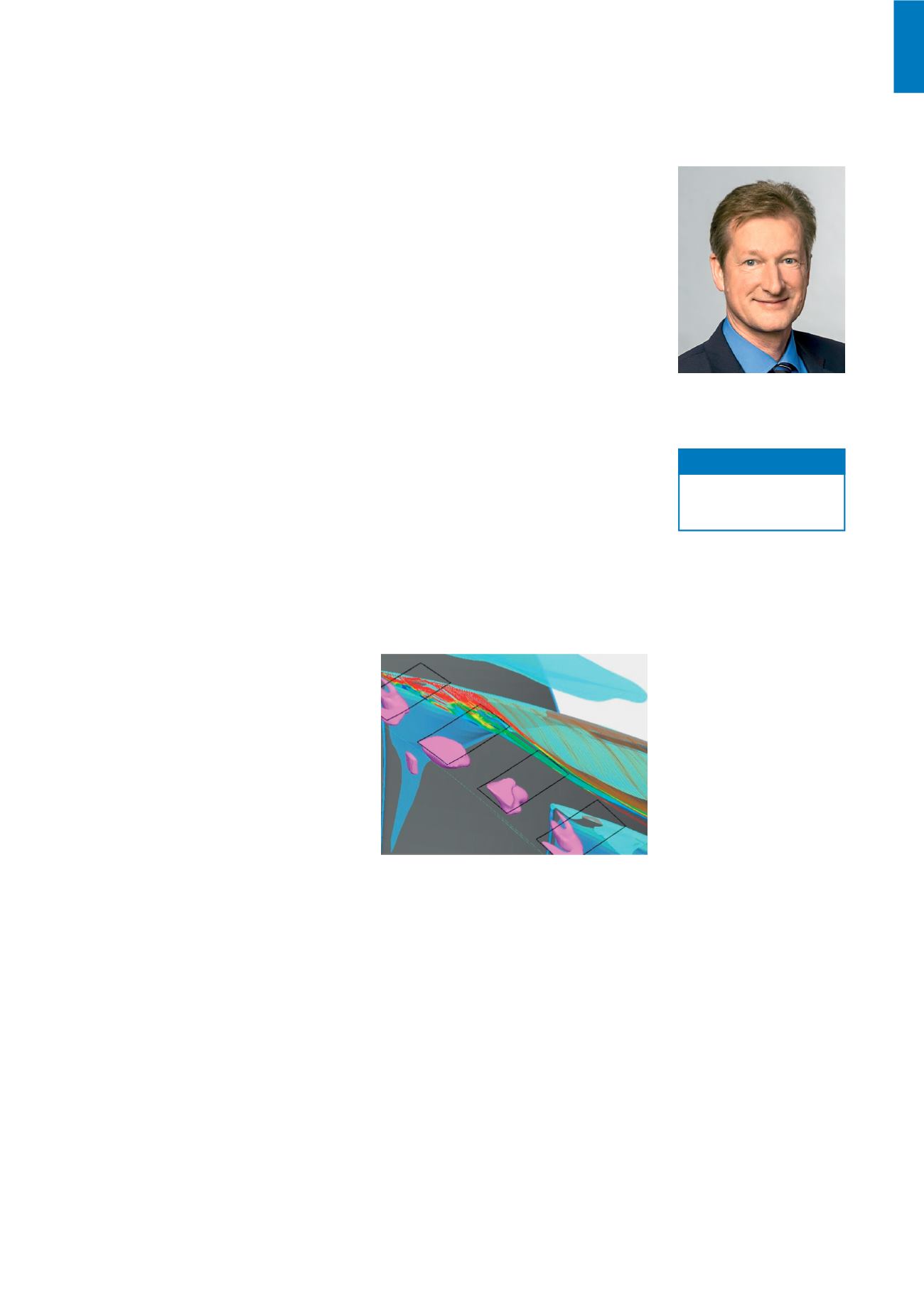
117
Turbomachinery and Flight Propulsion
Turbomachinery and Flight Propulsion
Experimental investigation and numerical simulation of
turbomachinery components and flight propulsion systems
Compressor Aerodynamics, Performance
and Operating Range Extension
The stability of transonic axial compres-
sors is mainly triggered by the tip gap flow
and its interaction with the passage main
flow. Several secondary flow phenomena
occur, e.g. shock-vortex interaction.
Casing treatments (CTs) have shown their
ability to enhance the stability of transonic
axial compressor rotors at near stall con-
ditions by influencing the near casing flow
field. CTs are applied over the compressor
rotor and can be designed differently, but all
of them energize the near casing flow field.
At the LTF, especially tip blowing (TBCT)
and axial slot casing treatments (AxCTs)
have been investigated. These CT types
recirculate flow from a downstream part
against the main flow direction in front
of the leading edge of the compressor
rotor. Besides a tremendous extension of
the operating range, studies at the LTF
have also shown a positive effect on the
peak efficiency point at design speed of
the treated rotor. Most of the previous
investigations have been carried out using
a rotor only model. To use CTs in real
applications, it is necessary to gain more
knowledge on how the CTs behave in a
multistage environment.
The focus of the present studies lies on
the influence of CTs on the stage match-
ing of a multi-stage compressor. For this
purpose, CFD studies are carried out for a
three-stage transonic axial compressor.
The unsteady interaction between main
flow and the exiting and re-entering treat-
ment flow is investigated using state of
the art phase lag simulations. The studies
are performed in close cooperation with
associated national research institutes and
industry partners.
n
Research activities of the Institute of Flight Propulsion in 2015 covered
topics in the fields of flight propulsion, gas turbines and thermal turboma-
chinery. Based on a long tradition the institute develops thermo-dynamic
engine models in order to investigate steady and unsteady gas turbine
engine and turbomachinery behavior.
Prof. Dr.-Ing.
Volker Gümmer
www.ltf.mw.tum.de sekretariat@ltf.mw.tum.dePhone +49.89.289.16164
Contact
The history of the Institute of Flight
Propulsion (LFA) reaches back to 1964,
when Prof. Münzberg was first appointed
head of the chair in downtown Munich.
Since its foundation the institute has been
dedicated to research and teaching in the
field of jet propulsion and gas turbines.
The institute is an active member of
national research associations, participant
in European research projects and long-
term partner of leading aero-engine and
component manufacturers. One highlight
is the framework agreement between the
Institute of Flight Propulsion/TUM, the
Bavarian Government and GE Global Re-
search Europe. The cooperation includes
the development of the world’s most
advanced high-speed research radial and
axial compressor laboratories focused on
developing tomorrow’s aircraft engines
and gas turbines. At the end of 2016 the
first test vehicle on the new axial com-
pressor testbed was commissioned and
tested at Garching.
Flow field visualization of an axial slot casing treatment
applied on a tip critical transonic compressor rotor:
flow with negative axial velocity component (blue),
streamlines of tip gap vortex, recirculated flow entering
the passage (red).