
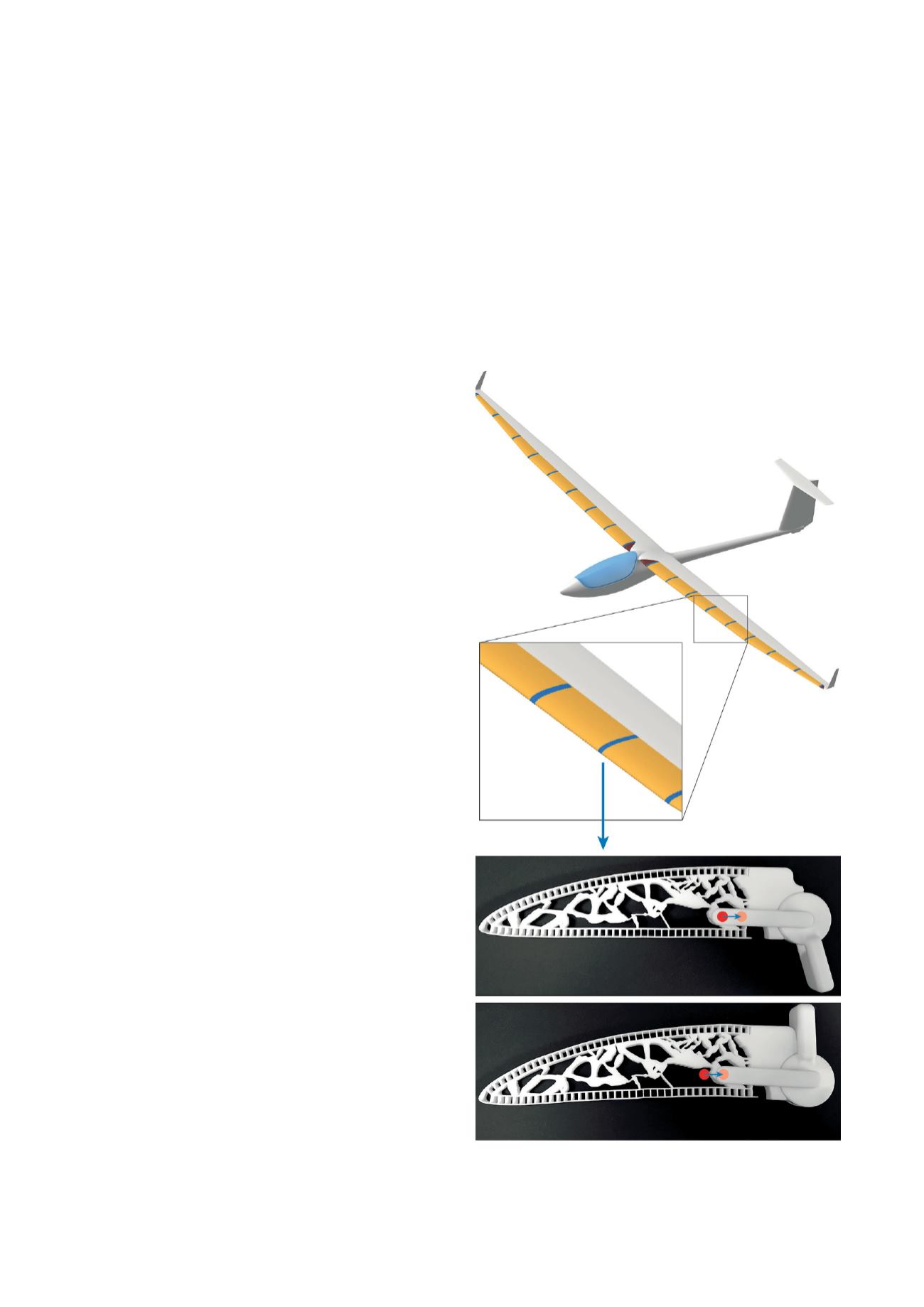
288
Product Development and Lightweight Design
Multi-disciplinary design, numerical optimization, modelling and simulation, design methods, tools and processes
n
Joining the two former laboratories for product development and lightweight design offers
great potential for research synergies.
In November 2017, the new laboratory was founded after
merging the two labs for product development and light-
weight structures. The two scientific disciplines provide
a good balance between similarities and differences for
synergy. They share a strong focus on engineering design
with a comprehensive and interdisciplinary view, and are
concerned with methods and tools to cope with com-
plexity. At the same time, they are different in breadth and
depth: while product development aims at applicability to
a broad range of technical disciplines, lightweight design
is about specific solutions to technical problems.
The accomplishments of both former labs in 2017 are
presented – for the last time in two separate parts.
In 2018, we will re-align research directions to optimally
combine the long and successful history of product devel-
opment and lightweight design at TUM with new impulses
from engineering science and needs from industry. The
primary focus of our future research will be on design and
optimization of complex technical systems in particular
form aerospace and automotive.
Part I: Lightweight Design
Morphing Wings
A concept for a morphing leading edge of a sailplane wing
is developed in the project MILAN. Preliminary studies
showed great potential for total aircraft drag decrease of
up to 12% compared to conventional designs by mor-
phing the front part of the wing in between a high speed
and a low speed, high lift configuration, thus mitigating
the design compromise for different speeds of a fixed
geometry configuration. The shape change from the
original high speed airfoil to the actuated low speed-high
lift airfoil is accomplished by deforming the wing shell
precisely using several spanwise arranged ribs, designed
as compliant mechanisms. Topology optimization is used
to generate the geometry of the compliant mechanism
ribs. First designs were accomplished using commercial
topology optimization software. Currently a new topology
optimization software environment is under development
including finite strain theory and stress constraints.
Project
■■
Milan (by Prof. Hornung)
Laser sintered concept study of a compliant mechanism actuation rib